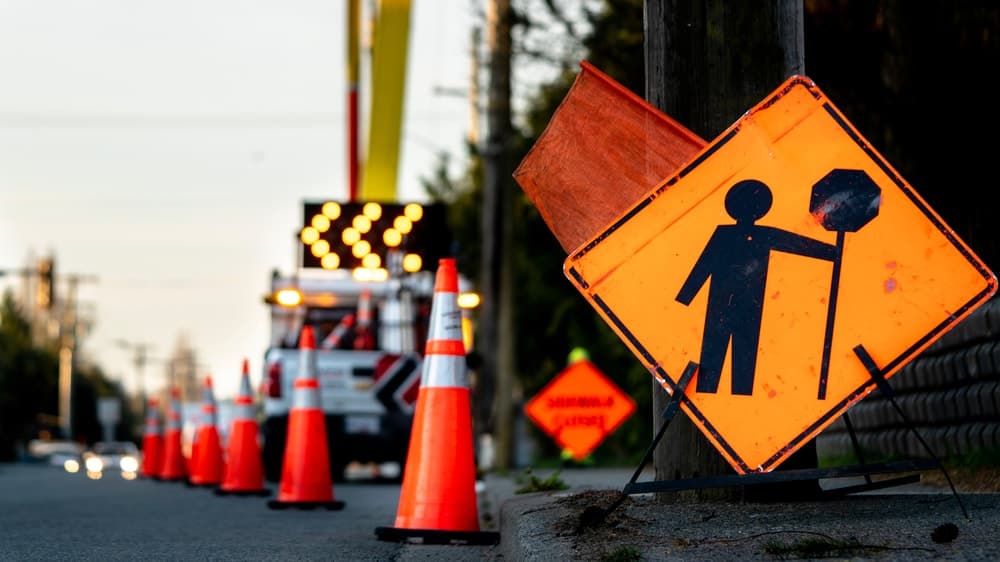
Since 1952, Logan Heating & Cooling has established itself as North Carolina’s premier HVAC and electrical contractor, earning BBB accreditation since 1972 with an A+ rating that speaks to their unwavering commitment to exceptional service.
As a Carrier factory-authorized dealer with NATE-certified technicians, Logan combines cutting-edge technology with old-school reliability – offering everything from 24/7 emergency repairs to complex commercial installations across the Piedmont Triad.
With more than 45 skilled technicians serving both residential and commercial clients, this 55-person team has built a reputation that turned a small family business into a regional leader over seven decades.
As Logan Heating & Cooling grew, the company had modernized its field operations using ServiceTitan to manage scheduling, dispatching, and job tracking. However, time tracking and payroll remained entirely manual, creating friction for both the office and the field.
Every technician filled out a paper timesheet each day, spending roughly 10 minutes per sheet. With 45 technicians, that totaled nearly eight hours a day, just on filling out timesheets. On top of that, dispatchers spent an additional four hours per day manually transferring those entries into Excel.
“The employees were tired of doing timesheets because it took so much time every week,” recalls Paula Kennedy, Controller at Logan Heating & Cooling. “It was really time-consuming for everyone involved.”
Beyond time investment, the lack of integration between systems created visibility gaps. Technicians never saw their total hours before payroll was processed. Managers couldn’t view labor data in real-time. Payroll relied on rounding hours to the nearest quarter and manual entry into their provider’s system, increasing the risk of errors and compliance issues.
When Logan evaluated the Miter and ServiceTitan integration, they saw an opportunity to overhaul a decades-old process.
With Miter and ServiceTitan working together, technicians now simply dispatch, arrive, and complete jobs in ServiceTitan, and those actions automatically generate timesheet data. FleetPro also adds GPS-based accuracy. Managers review and approve timesheets in Miter or ServiceTitan, and once finalized, the data syncs directly with Sage Intacct for payroll and job costing.
But Miter is doing more than just syncing time – it’s streamlining several time-consuming administrative tasks that used to rely on manual work and Excel spreadsheets.
Miter now handles time tracking, payroll, compliance, and HR – while syncing data back into Sage Intacct to power more accurate job costing and financial reporting.
Logan follows two separate overtime policies: install technicians have overtime spread across all their jobs for the week (not just the last job), and service technicians earn overtime for after-hours calls. These used to be calculated manually. Now, Miter handles it all, saving dispatchers 1.5 hours each week.
Miter enforces Logan’s policy of capping unpaid “dead time” at 30 minutes per day, ensuring accurate labor tracking even when technicians forget to clock in or out.
Technicians now see their hours in ServiceTitan and again in Miter, giving them confidence they’re being paid accurately and helping the office spot and correct errors before payroll runs.
When Logan employees elect benefits through UnitedHealthcare, Miter then updates deduction amounts, completely eliminating manual entry. Paula says it saves about 30 minutes per new employee and reduces the risk of errors.
Logan is also using Miter’s integration with Checkr for drug testing, background checks, and MVR screenings as part of their hiring and onboarding process.
The transformation at Logan Heating & Cooling has been remarkable, with benefits extending across every department in the organization.
Each of Logan’s 45 technicians had been spending about 10 minutes per day filling out paper timesheets, adding up to nearly eight hours of lost time per day. Then a CSR would spend another four hours daily manually entering those timesheets into Excel. Add in the admin team’s weekly timesheet compilation process, and Logan was losing more than 60 hours every week to paperwork alone.
Miter streamlined all of it. Now, when technicians dispatch themselves to a job in ServiceTitan, arrive at the job site, and mark the job as complete, all that time information feeds into Miter.
“Where we really see the time savings is with our admin staff. Just eliminating manual timesheet compilation has saved about eight hours per week,” Paula says.
In the field, adoption has gone smoothly. Technicians embraced the workflow of dispatching, arriving, and completing jobs in ServiceTitan, which results in timesheet accuracy in Miter.
The system is forgiving of small errors. “Every now and then a tech will forget to dispatch themselves until they arrive at the job,” Paula says. “But anyone in the office – CSRs or managers – can easily make that correction.”
The integration has significantly increased both oversight and transparency.
“It has three layers of approval before it gets to Miter,” Paula notes. “So we know that managers are reviewing and approving the timesheets before they’re submitted.”
At the same time, technicians now have real-time visibility into their hours, both in ServiceTitan and Miter.
“What’s nice is that technicians can now see their total weekly hours in ServiceTitan, and when that data comes over to Miter, they can see the exact same detail there too,” Paula says.
To further ensure accuracy, Logan set up guardrails in ServiceTitan and Miter. If a technician forgets to clock into a job, they must record time against another category, such as drive time, admin, or a break. And Miter enforces Logan’s policy that limits unpaid “dead time” to a maximum of 30 minutes per day.
“We make sure all time is accounted for,” Paula explains. “They can’t get paid if they just forget to clock out at the end of the day.”
Because of this visibility, last-minute corrections and issue resolution are also much easier. “We can see everything, so it makes it easy to make any last-minute corrections or to identify issues,” Paula says. “Plus, the technician can see those details as well to assure them they are being paid for every minute of work.”
The benefits extend beyond time tracking to encompass Logan’s entire payroll and accounting process. Information flows seamlessly from ServiceTitan to Miter, then syncs with Sage Intacct.
“After payroll has been processed, that information gets fed over to Intacct automatically,” Paula explains. “It has greatly reduced the work for us.”
Previously, Paula’s team manually created journal entries for each payroll run, which took about 30 minutes each cycle. Now those entries are generated automatically, saving time and improving accuracy.
The integration also ensures data consistency across systems. If a correction is needed, Paula can make changes directly in Miter, and the journal entry is regenerated and synced with Intacct.
Thanks to the integrated system, Logan now has complete visibility into project labor costs, including time, overtime, and benefits. This level of insight helps them price future work more accurately and identify which types of jobs are most profitable.
Logan’s experience with Miter’s implementation exceeded expectations, with Paula finding the onboarding process straightforward and well-supported.
“Onboarding was very simple,” Paula explains. “Mike, my launch manager, was very responsive anytime I had a question and would respond right away.”
One standout feature of the implementation was Miter’s approach to training documentation. All implementation sessions were recorded and bookmarked by topic, giving Logan a library of on-demand resources they still reference today.
The recordings continue to be a valuable resource, especially as the team explores more Miter features or brings new staff up to speed.
The combination of strong support and thorough documentation helped Logan hit the ground running and take full advantage of the ServiceTitan-Miter integration right from day one.
For other ServiceTitan customers considering the Miter integration, Paula offers this advice: embrace the opportunity to improve how your team works.
“You have to understand that the way we had done payroll had been done this way for decades – literally decades,” she says. “So we had to teach ourselves that it’s okay to move into the 21st century. Once you embrace everything Miter can do, it will make your life so much simpler and easier.”
The transformation didn’t happen overnight, but the results – better oversight, fewer errors, and major time savings – made it clear they’d made the right move.
With their time tracking and payroll processes streamlined, Logan Heating & Cooling is better positioned to grow efficiently and sustainably. The ServiceTitan-Miter integration has removed hours of manual work each week while increasing accuracy and visibility across the business.
“It is really hands-off now,” Paula reflects. “The same information that is in ServiceTitan can be seen in Miter. It’s to that level of detail and it’s so easy to match it up.”
The transformation has freed up valuable time across the organization, allowing Logan’s team to focus on higher-value work while maintaining the oversight and control they need.
“I can’t say enough good things about it,” Paula concludes. “It’s been so much better.”